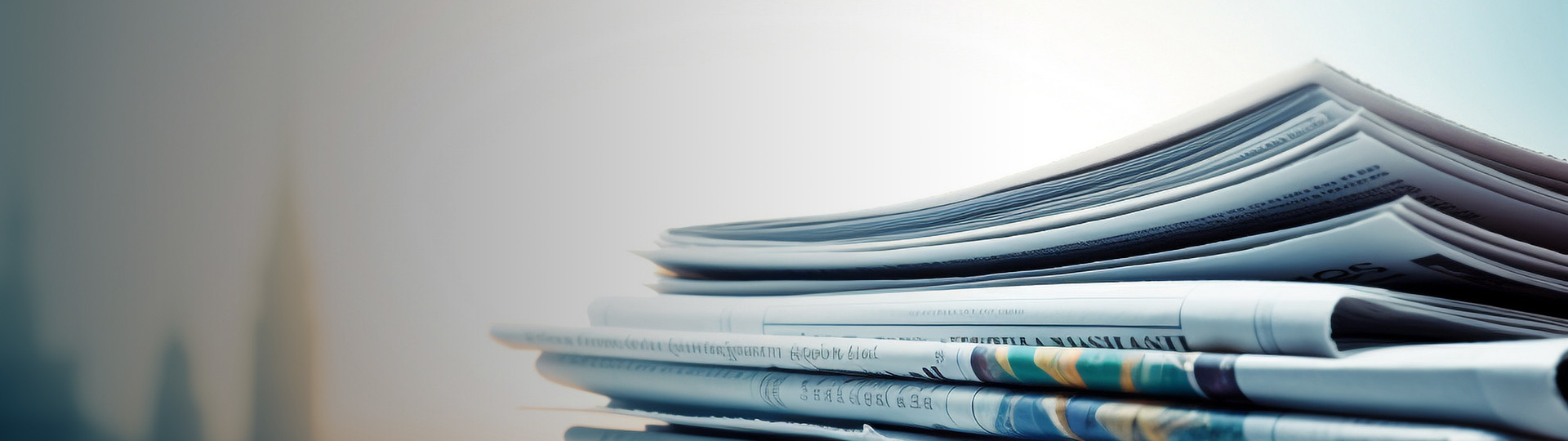
Real-time tracking industry hot spots, share authoritative information, help you grasp business opportunities
What are the main equipment of the rolling mill?
Release Date:
2024-04-29
1. Working machine base It is composed of roll, rolling mill housing, bearing package, bearing, worktable, rolling guide, rail seat, roll adjusting device, upper roll balancing device and roll changing device, etc.
1. Working machine base
It is composed of roll, rolling mill housing, bearing package, bearing, worktable, rolling guide, rail seat, roll adjusting device, upper roll balancing device and roll changing device, etc.
2. Roll
It is a component that plastically deforms metal (see roll).
3. Roller bearing
The rolls are supported and held in a fixed position in the stand. The working load of the roll bearing is heavy and changes greatly, so the bearing friction coefficient is required to be small, have sufficient strength and rigidity, and be easy to replace the roll. Different types of roll bearings are used for different rolling mills. The rigidity of rolling bearing is large, the friction coefficient is small, but the pressure bearing capacity is small, and the external dimension is large, and it is mostly used for the work roll of plate and strip rolling mill. Sliding bearings have two kinds of semi-dry friction and liquid friction. Semi-dry friction roller bearings are mainly bakelite, copper tile and nylon tile bearings, which are relatively cheap and are mostly used in profile rolling mills and billet machines. There are three types of liquid friction bearings: dynamic pressure, static pressure and static-dynamic pressure. The advantages are that the friction coefficient is relatively small, the pressure-bearing capacity is large, the working speed is high, and the rigidity is good. The disadvantage is that the thickness of the oil film changes with the speed. Liquid friction bearings are mostly used for plate and strip rolling mill backup rolls and other high-speed rolling mills.
4. Rack
It is composed of two "archways" to install the roll bearing seat and roll adjustment device, which must have sufficient strength and rigidity to withstand the rolling force. Rack form is mainly closed and open two. The closed frame is an integral frame with high strength and rigidity. It is mainly used for rolling mills and strip mills with large rolling forces. The open frame is composed of a frame body and an upper cover, which is convenient for changing rolls and is mainly used for horizontal profile rolling mills. In addition, there is a mill without a memorial arch.
5. Rail base
Used to install the rack, and fixed on the foundation, also known as the foot plate. Withstand the gravity and tilting moment of the working machine base, and ensure the accuracy of the installation size of the working machine base.
6. Roll adjustment device
It is used to adjust the roll gap to make the rolled piece reach the required section size. The upper roller adjustment device is also called "pressing device", which has three types: manual, electric and hydraulic. The manual pressing device is mostly used in profile mills and small mills. The electric depressing device includes components such as a motor, a reducer, a brake, a depressing screw, a depressing nut, a depressing position indicator, a spherical cushion block, a load gauge, etc. Its transmission efficiency is low, the rotational inertia of the moving part is large, the reaction speed is slow, and the adjustment accuracy is low. Since the 1970 s, after AGC (automatic thickness control) system has been adopted for plate and strip rolling mills, hydraulic pressure reduction devices have been adopted for new strip cold and hot rolling mills and thick plate rolling mills, which have the advantages of small plate thickness deviation and high product qualification rate.
7. Upper roll balancing device
A device used to lift the upper roll and prevent the rolled piece from being impacted when entering and leaving the roll. The forms are: spring type, mostly used in profile rolling mills; heavy hammer type, commonly used in primary rolling mills with large roll movement; hydraulic type, mostly used in four-roll strip rolling mills.
In order to improve the operating rate, the rolling mill is required to change rolls quickly and conveniently. There are four types of roller changing methods: C- shaped hook type, sleeve type, trolley type and roller changing type. The first two methods of changing rolls are assisted by cranes, while the whole frame needs two sets of stands for changing rolls. This method is mostly used in small rolling mills. The trolley roll change is suitable for large rolling mills and is conducive to automation. Nowadays, the rolling mill adopts a fast automatic roll change device, and it only takes 5 to 8 minutes to change the roll once.
8. Transmission device
It is composed of motor, reducer, gear seat and connecting shaft. The gear seat divides the transmission torque to two or more rolls.
Auxiliary equipment includes equipment for a series of auxiliary processes in the rolling process. Such as raw material preparation, heating, steel turning, shearing, straightening, cooling, flaw detection, heat treatment, pickling and other equipment. Lifting and transportation equipment, cranes, transporters, roller tables and transfer machines, etc.
9. Ancillary equipment
There are equipment for supply, distribution, roller grinding, lubrication, supply and drainage, fuel supply, compressed air, hydraulic pressure, removal of scale, machine repair, electrical repair, acid removal, recovery of oil, water and acid, and environmental protection.
Key words:
Weldments
Iron castings
Related News
Contact Us
Contact Phone:+863583912665
Mobile:+8618334873442 +8613994825542
Fax:+863583912665
E-mail:lyq@sxxrdyj.cn
Address: Xifenyang Village Industrial Park, Jiaocheng County, Shanxi Province