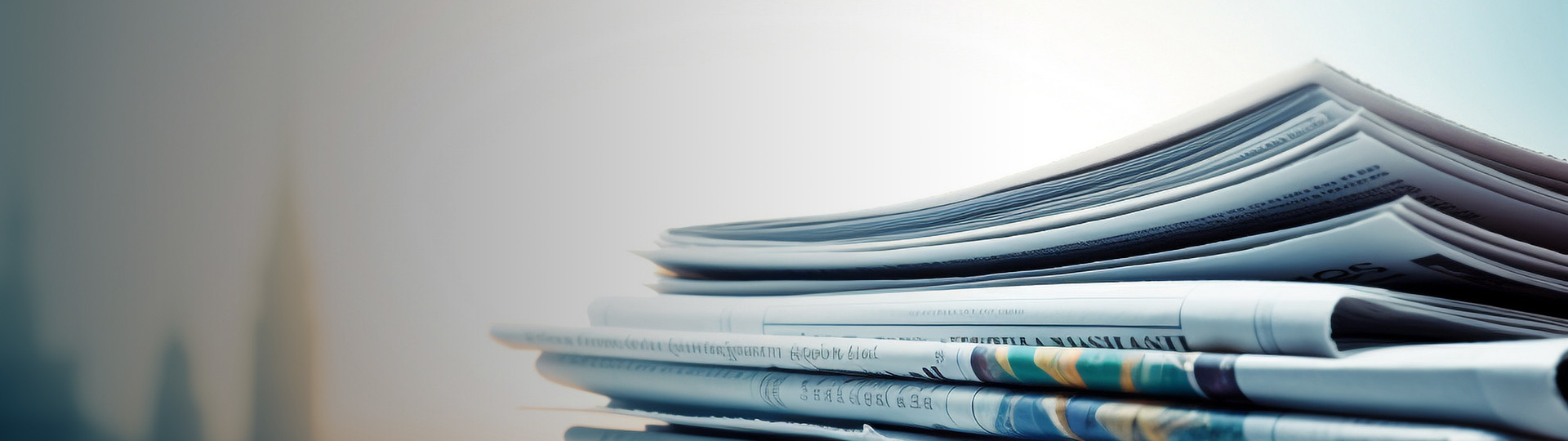
News
Real-time tracking industry hot spots, share authoritative information, help you grasp business opportunities
Common problems and solutions of iron castings
Release Date:
2024-05-25
This article will discuss the common problems and solutions in the use of iron castings to help readers better understand and deal with the technical problems related to iron castings.
As a common metal product, iron castings are widely used in industrial production, construction equipment and many other fields. However, in the process of use, iron castings will also have some common problems, which need to be solved in time.
First of all, one of the common problems of cast iron is porosity. Porosity will cause uneven internal quality of cast iron parts, affecting its strength and appearance. Solutions include optimizing the melting process, controlling the pouring temperature and speed, etc., which can effectively reduce the formation of pores.
Secondly, surface defects are also one of the common problems of cast iron. Surface defects such as bubbles, oxide scale, etc. adversely affect the appearance and performance of cast iron parts. The main methods to eliminate surface defects are to improve the quality of sand molds, control the pouring temperature and metal pouring speed.
In addition, the deformation of cast iron parts also needs attention. In the casting process, the cast iron is susceptible to thermal stress and deformation. In order to avoid deformation of cast iron parts, measures such as preheating sand mold, reasonable design of gate and increase of body thickness can be taken.
In summary, in view of the common problems in the use of iron castings, through optimizing the process, strengthening quality control and taking effective preventive measures, the quality and performance of iron castings can be improved, its service life can be extended, and its safety and reliability in engineering can be ensured.
First of all, one of the common problems of cast iron is porosity. Porosity will cause uneven internal quality of cast iron parts, affecting its strength and appearance. Solutions include optimizing the melting process, controlling the pouring temperature and speed, etc., which can effectively reduce the formation of pores.
Secondly, surface defects are also one of the common problems of cast iron. Surface defects such as bubbles, oxide scale, etc. adversely affect the appearance and performance of cast iron parts. The main methods to eliminate surface defects are to improve the quality of sand molds, control the pouring temperature and metal pouring speed.
In addition, the deformation of cast iron parts also needs attention. In the casting process, the cast iron is susceptible to thermal stress and deformation. In order to avoid deformation of cast iron parts, measures such as preheating sand mold, reasonable design of gate and increase of body thickness can be taken.
In summary, in view of the common problems in the use of iron castings, through optimizing the process, strengthening quality control and taking effective preventive measures, the quality and performance of iron castings can be improved, its service life can be extended, and its safety and reliability in engineering can be ensured.
Key words:
Weldments
Iron castings
Related News
Contact Us
Contact Phone:+863583912665
Mobile:+8618334873442 +8613994825542
Fax:+863583912665
E-mail:lyq@sxxrdyj.cn
Address: Xifenyang Village Industrial Park, Jiaocheng County, Shanxi Province
Business License